Improve the quality of your continuous casting process!
In order to achieve highest yield of prime quality products a very tight control of caster boundary conditions is required. One key aspect is to balance the application of inert gas into the casting channel.
The aim should be to use smallest argon quantities possible in order to avoid sliver defects in the mould but high enough to combat alumina clogging in the casting channel being able to cast the targeted sequence length.
Using gas purged Stopper for steel flow control, one major factor is to maintain a positive backpressure at a stable inert gas flowrate in the argon line to avoid ingress of air into the gas line and casting channel.

Using gas purged Stopper for steel flow control, one major factor is to maintain a positive backpressure at a stable inert gas flowrate in the argon line to avoid ingress of air into the gas line and casting channel.
This requirement can be achieved by a customized pressure device in the refractory embodiment:
RHI Magnesita’s SHP stopper technology
Discover how bubble dispersion in the nozzle makes a substantial difference
The bubble dispersion is one of the key factors in order to avoid formation of defects in the mould.
See what kind of difference different stoppers make in the following water models:
The bubble dispersion is one of the key factors in order to avoid formation of defects in the mould.
See what kind of difference different stoppers make in the following water models:
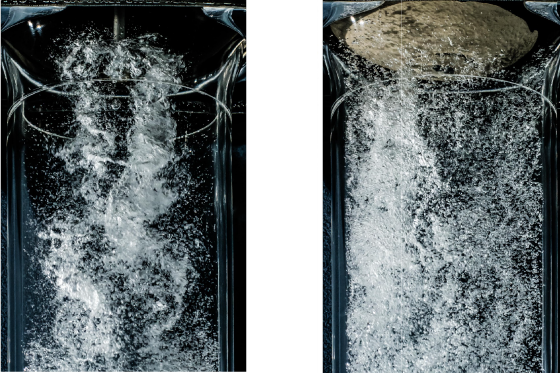
Conventional argon stopper
- Provides unsteady gas distribution below the throttle point.
- At lower gas flow rates unfavourable flow patterns in the nozzle can occur resulting in bubble bursting effects and perturbations of the liquid metal level in the mould.
- Flow transitions from bubbly to slug flow can occur with strong pressure fluctuations causing flow pattern changes in the mould.
SHP-Stopper
- The generation of even bubble distribution across the cross section of the casting channel also at reduced argon flow rates.
- The “softer jets” generated by improved bubble distribution from the SHP-stopper explain a more stable flow performance over the entire range of different casting conditions.
- The even bubble distribution is finally leading to reduced slag entrapment and better surface quality of IF steel grades.
- SHP stoppers can be used for Ca-treated steel grades as well. Steel quality levels on these grades are comparable to a standard stopper.
Key features of RHI Magnesita’s SHP-Stopper technology
- X-Spring Gas-tight Fixing System
expanding graphite cartridge counteracts thermal expansion of metal fixing rod to maintain gas-tightness
- Directional Porosity Plug (DPS)
with calibrated bore to maintain positive argon backpressure in the system
- Clean Stream Cartridge (CSC)
cleans the argon stream of any gaseous contaminants deriving from the refractory thereby avoiding blockage by condensation products in the argon outlet
- Slot Hole Plug (SHP)
improves the gas distribution at stopper nose and casting channel leading to less disturbances in the mould and reduced nozzle clogging
RHI Magnesita’s SHP-Stopper
SHP-Stopper
- The generation of even bubble distribution across the cross section of the casting channel also at reduced argon flow rates.
- The “softer jets” generated by improved bubble distribution from the SHP-stopper explain a more stable flow performance over the entire range of different casting conditions.
- The even bubble distribution is finally leading to reduced slag entrapment and better surface quality of IF steel grades.
- SHP stoppers can be used for Ca-treated steel grades as well. Steel quality levels on these grades are comparable to a standard stopper.
Key features of RHI Magnesita’s SHP-Stopper technology
- X-Spring Gas-tight Fixing System
expanding graphite cartridge counteracts thermal expansion of metal fixing rod to maintain gas-tightness
- Directional Porosity Plug (DPS)
with calibrated bore to maintain positive argon backpressure in the system
- Clean Stream Cartridge (CSC)
cleans the argon stream of any gaseous contaminants deriving from the refractory thereby avoiding blockage by condensation products in the argon outlet
- Slot Hole Plug (SHP)
improves the gas distribution at stopper nose and casting channel leading to less disturbances in the mould and reduced nozzle clogging
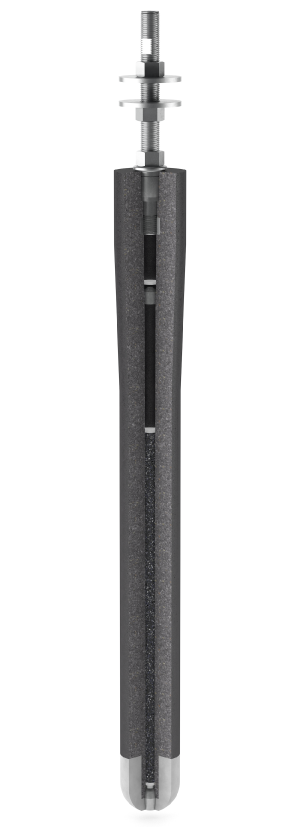
RHI Magnesita’s SHP-Stopper
Get more information
An expert dedicated to your area will get in touch with you.
If you have any questions, do not hesitate to contact us.