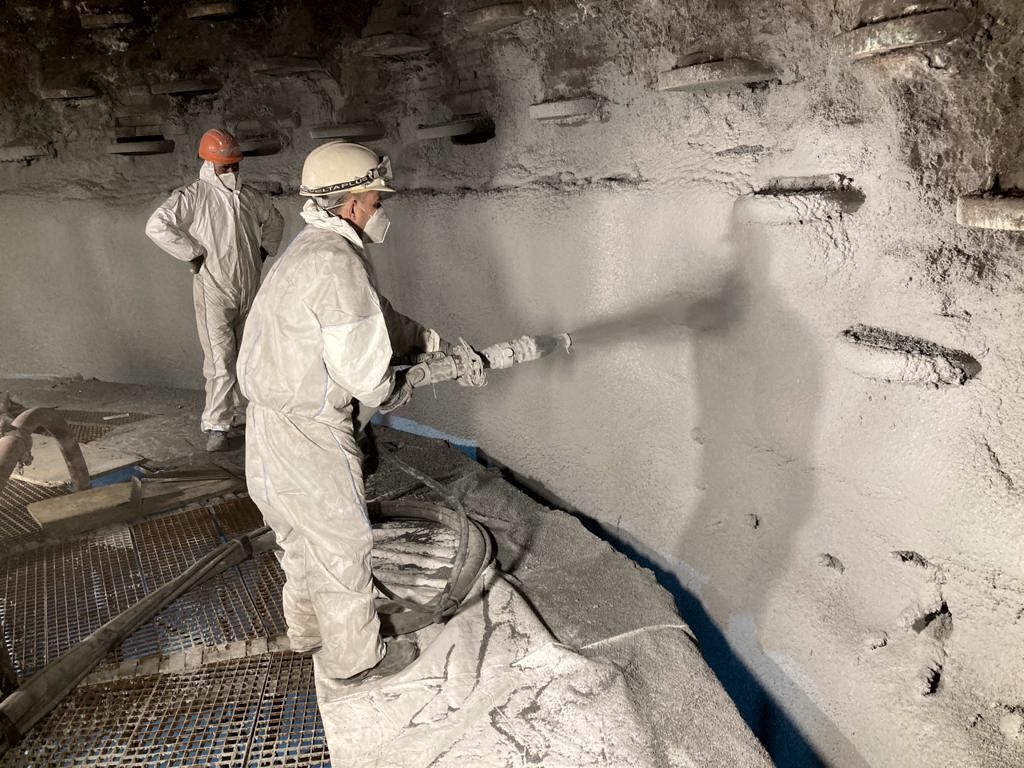
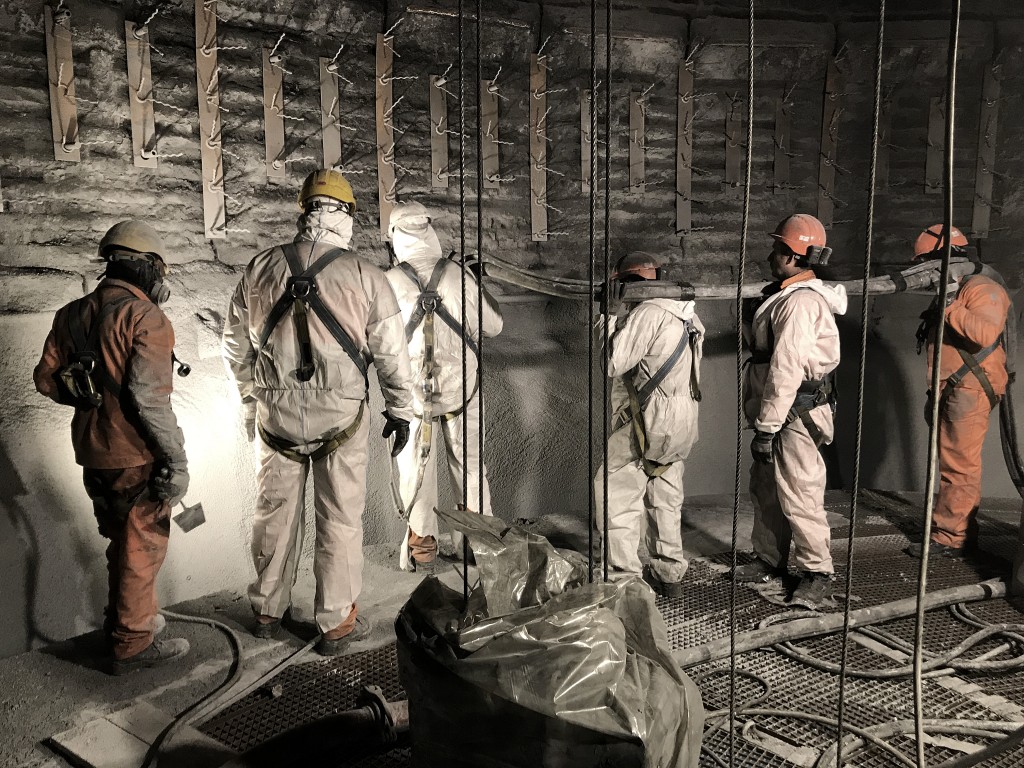

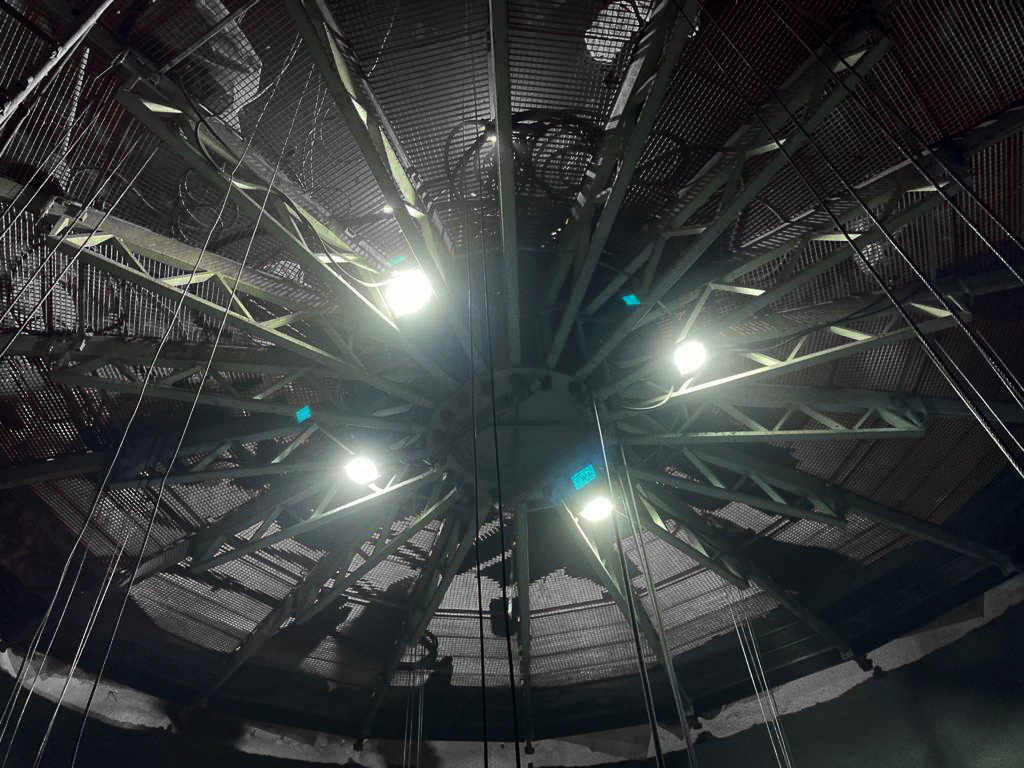

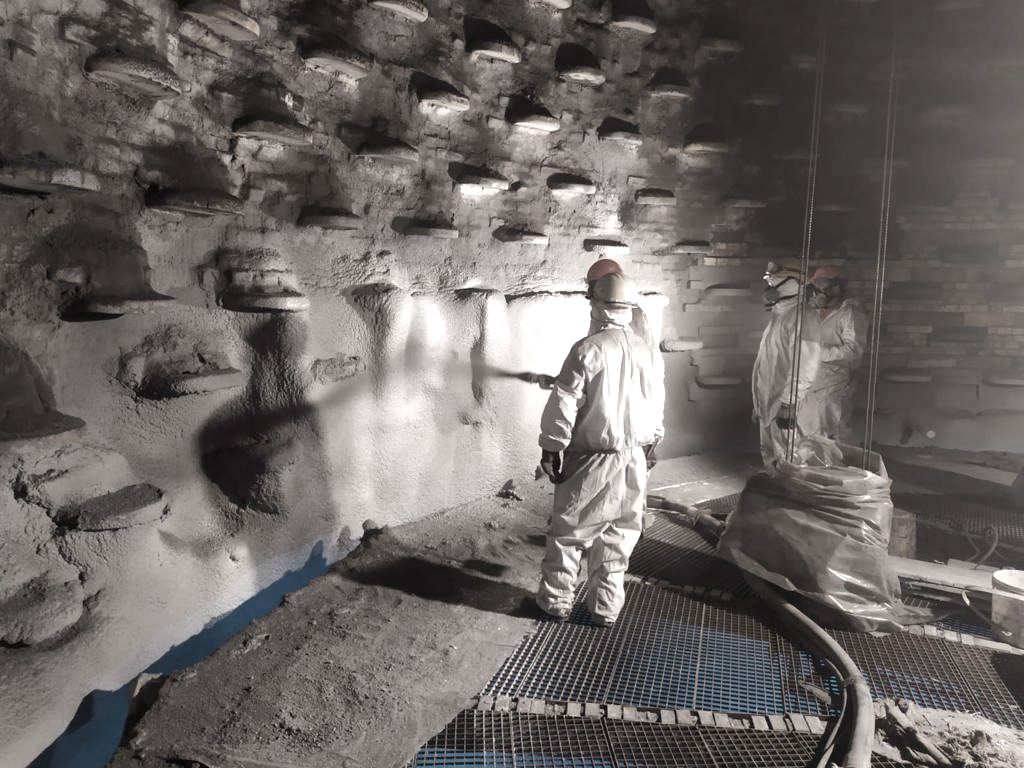
The history of Alumina Monolithic Solutions & Ironmaking can be seen as the long list of our successfully completed installations.
At the core, each of our installations is an intervention – a disruption of the normal workflow in a factory.
Every time refractory materials are applied, it means downtime, and we therefore keen to make our interventions as fast as possible to limit the downtime of our clients’ costly operations.
In addition, our installations must be performed with the goal of utmost safety and longevity.
Nobody wants to conduct a repair that only calls for another repair in the short term.
As we are a supplying to key industries such as the production of iron, steel, cement, aluminium and other essential materials, we are not speaking about just any sort of production.
By definition, our refractory materials are used under extreme circumstances: extremely high temperatures, extreme temperature changes, extreme attacks by chemicals or physical adversities. In the absence of these extreme conditions, our customers would not need our advanced refractories – they could make do with more or less any old material, for example regular cement.
But since conditions are extreme by the very nature of our clients’ production circumstances,the installation of our products is of equally high importance.
When needed, our Research & Development teams push the perfomance parameters of our refractories by coming up with innovative cement-free formulations.
In our projects, we therefore never simply supply a material – deliver some palettes, big bags or individually packaged refractories and not worry about their future fate. Instead, we carefully investigate the situation at hand and we select the most suitable material in tandem with the optimal installation techniques.
Alumina Monolithic Solutions & Ironmaking has full command of the entire range of application techniques available for refractory installations. Our teams perform applications by casting, gunning, shotcreting, and ramming on an almost daily basis. Our Seven Cem, Seven Dry, Seven Plast, Seven Trow, and Sevenlite products complement the portfolio and demand a whole array of installation knowledge in themselves.
When needed, our Research & Development teams push the perfomance parameters of our refractories by coming up with innovative cement-free formulations.
We have developed and manufactured a comprehensive range of installation equipment: robots and mixers for shotcreting, gunning, casting, flow and other applications.
With these specialized tools and our engineering knowledge we are a single-stop contact for complex customer-specific projects.
If we don’t find existing methods satisfactory enough, we take the liberty of developing new ones. One prime example is our shotcreting methodology for steel ladle management, which allows for linings to be potentially endless – instead of a series of disruptive repairs. Another innovative method combining several approaches is our Modular Hearth Shield