Desculpe, este conteúdo só está disponível em English e Deutsch. Por uma questão de conveniência para o utilizador, o conteúdo é mostrado abaixo no idioma por omissão para este site. Pode clicar numa das ligações para mudar o site para outro idioma disponível.
Maximize your metallurgical results with INTERSTOP inert gas purging systems!
Increased product requirements in terms of clean steel, very low carbon steel grades and clean copper require optimized process operation with bottom purging systems in converters, furnaces and ladles such as at EAF, BOF, LF and VD.
RHI Magnesita Switzerland offers gas control boxes for inert gas purging systems to propel your metallurgical results to a next level. The result of our innovative gas control box concept is an improved distribution of temperature as well as alloying elements in the melt. Especially the number, type, arrangement and quality of plugs, flow patterns as well as purging gases and their control exert a remarkable influence on the metallurgical process of our customers.
See how it works
Your benefits at a glance
- RHI Magnesita`s holistic system approach combines metallurgical know-how, gas control systems and refractory purging products
- State of the art system components to drive the process as close as possible to the metallurgical needs
- Extensive know how available for steel- and non-ferrous purging and shielding applications
- Latest IT solutions capable of complex operations to provide a high-level operator interface
- Maintenance friendly design for highest reliability
- Interstop and RHI Magnesita`s holistic system approach combines metallurgical know-how, gas control systems and refractory purging products
- State of the art system components to drive the process as close as possible to the metallurgical needs
- Extensive know how available for steel- and non-ferrous purging and shielding applications
- Latest IT solutions capable of complex operations to provide a high-level operator interface
- Maintenance friendly design for highest reliability
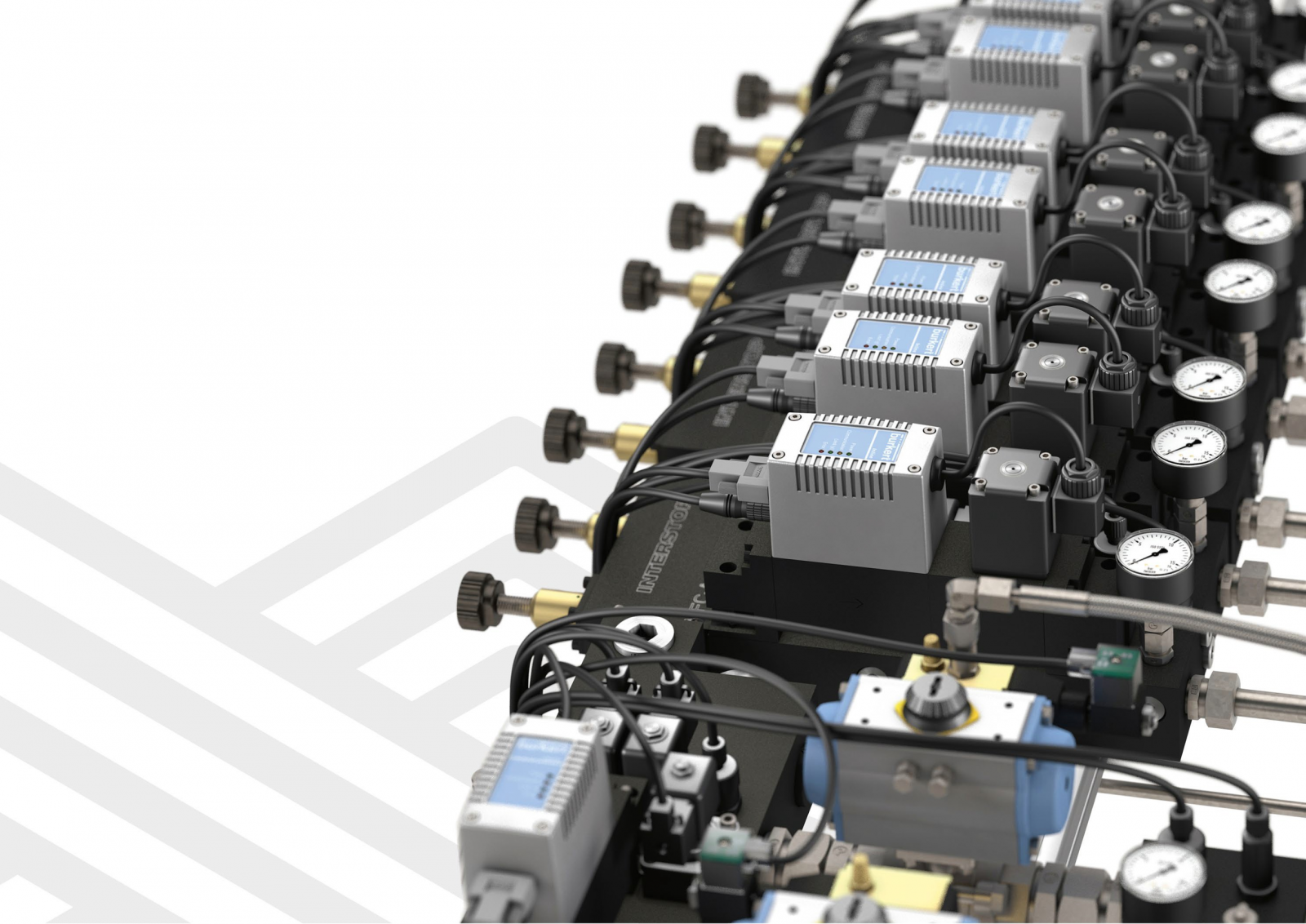
INTERSTOP® DPP gas purging system for EAF
The heart of the Direct Purging Plug system (DPP) is the gas control box, in which argon and nitrogen are precisely controlled. Special features of our mass flow controllers are the high precision of +/- 1.5% of the flow rate and the short setting time of less than 500 milliseconds.
In addition to the gas control unit, the DPP system includes the integration of process control, RHI Magnesita`s Direct Purging Plugs, a user-friendly HMI interaction and process visualization.
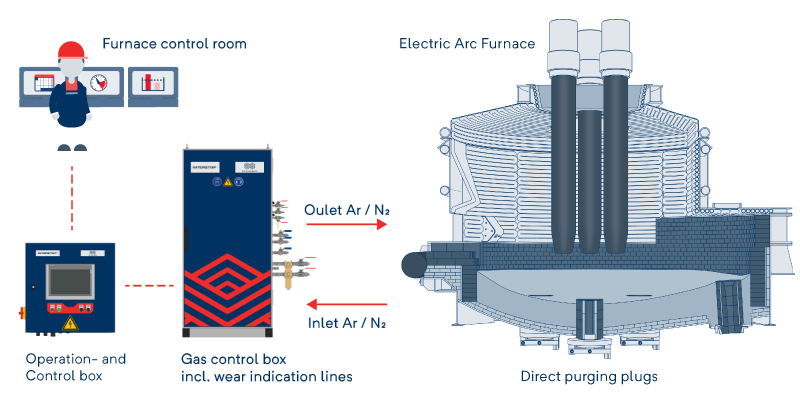
1
Furnance Control Room
Control over the entire gas purging
process and technology from refractory
to valve control and purging strategy.
2
Operation- and Control box
User-friendly visualization allowing setting of gas flow, gas type, operational mode and easy monitoring of system condition.
3
Gas Control Box incl. wear indication lines
Compact box with modular components, including the mass flow controllers and the electrical system with a rapid reaction of mass flow controllers (90% set flow within 2s) and high precision of mass flow (+/- 1.5%).
4
Direct purging plug
Efficient steel melt mixing in the lower and upper bath using gas purging plugs in the EAF heart, leading to process improvement, energy savings and alloy savings.
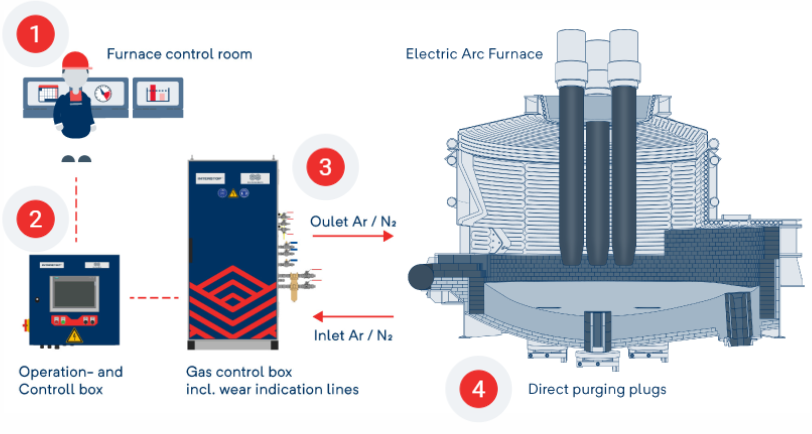
1. Furnance Control Room
Control over the entire gas purging process and technology from refractory to valve control and purging strategy.
2. Operation- and Control box
User-friendly visualization allowing setting of gas flow, gas type, operational mode and easy monitoring of system condition.
3. Gas control box
Compact box with modular components, including the mass flow controllers and the electrical system. Rapid reaction of mass flow controllers (90% set flow within 2s) and high precision of mass flow (+/- 1.5%). Process safety is increased with the wear indication lines (show when minimum brick length is reached). Gas supply and control of up to 6 purging plugs for electric arc furnaces with tap weights of up to 300t.
4. Direct purging plug
Efficient steel melt mixing in the lower and upper bath using gas purging plugs in the EAF heart, leading to process improvement, energy savings and alloy savings.
INTERSTOP® CLP gas purging system for Ladle
In addition to the same advantages given with the EAF system, additional features of the Controlled Ladle Purging system (CLP) concern the following supporting systems:
- the SOC-H system, which is a combination of a mechanical closure system with the gas purging plug providing maximum safety against breakout.
- the PFD plug function device for checking the purging plug on the preparation surface to ensure the release only of ladles with a properly functioning purging plug from the preparation surface.
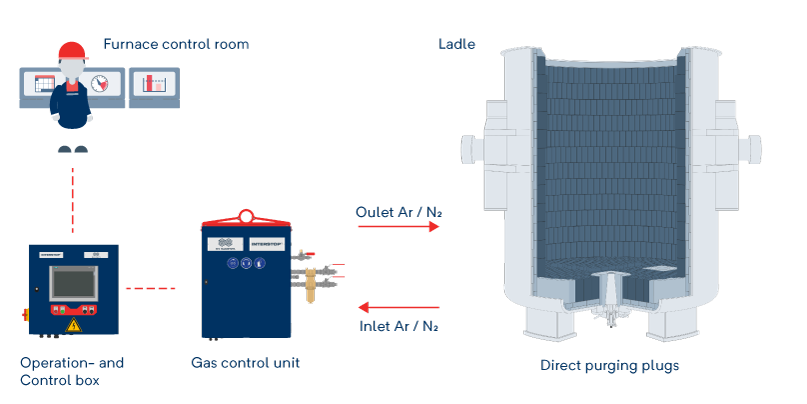
1
Furnance Control Room
Control over the entire gas purging
process and technology from refractory
to valve control and purging strategy.
2
Operation- and Control box
User-friendly visualization allowing setting of gas flow, gas type, operational mode and easy monitoring of
system condition. 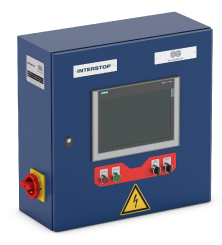
3
Gas control box
Compact box with modular components including the mass flow controllers. Rapid reaction of mass flow controllers (90% set flow within 2s) and high precision of mass flow (+/- 1.5%). Gas supply and control of up to 4 purging plugs and for ladles with tap weights of up to 350t.
4
Purging plugs
Efficient steel melt mixing, leading to higher process control, increase in productivity and improved metallurgical results.
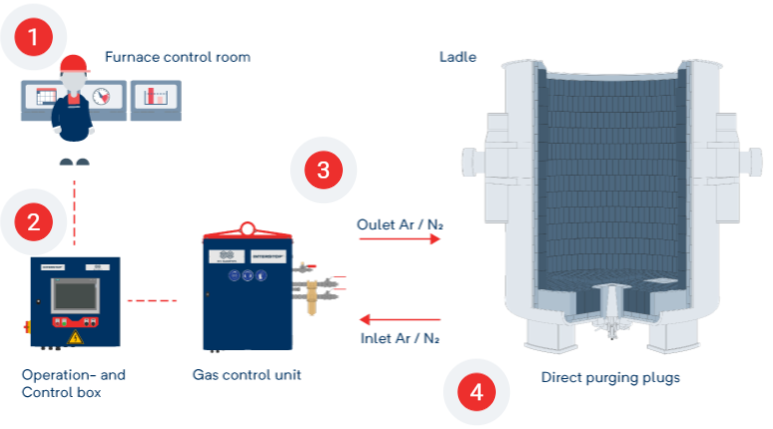
1. Furnance Control Room
Control over the entire gas purging process and technology from refractory to valve control and purging strategy.
2. Operation- and Control box
User-friendly visualization allowing setting of gas flow, gas type, operational mode and easy monitoring of system condition.
3. Gas control box
Compact box with modular components including the mass flow controllers. Rapid reaction of mass flow controllers (90% set flow within 2s) and high precision of mass flow (+/- 1.5%). Gas supply and control of up to 4 purging plugs and for ladles with tap weights of up to 350t.
4. Purging plugs
Efficient steel melt mixing, leading to higher process control, increase in productivity and improved metallurgical results.
Benefits of gas control box
- Wide regulation ratio 1 ÷ 50 of the mass flow controller (e.g. from 24 Nl/min to 1’200 Nl/min)
- Fast step response of the MFC (5% – 95% in less than 1 second)
- High accuracy of the MFC ±1.5% o.R. ±0.3% F.S. (o.R.: of reading; F.S.: of full scale)
- O-ring sealed components, maintenance friendly
- No instrument air required
- Low maintenance costs

Benefits of gas control box
- Wide regulation ratio 1 ÷ 50 of the mass flow controller (e.g. from 24 Nl/min to 1’200 Nl/min)
- Fast step response of the MFC (5% – 95% in less than 1 second)
- High accuracy of the MFC ±1.5% o.R. ±0.3% F.S. (o.R.: of reading; F.S.: of full scale)
- O-ring sealed components, maintenance friendly
- No instrument air required
- Low maintenance costs
Benefits of bottom purging system
- Minimization of the tap-to-tap time
- Less alloy elements required (cost saving)
- Less deoxidation agents (e.g. A1) required
- Shorter and quicker reaction pathways between the slag and steel bath
- Improved process control (higher accuracy of the tapping temperature and element levels)
Benefits of bottom purging system
- Minimization of the tap-to-tap time
- Less alloy elements required (cost saving)
- Less deoxidation agents (e.g. A1) required
- Shorter and quicker reaction pathways between the slag and steel bath
- Improved process control (higher accuracy of the tapping temperature and element levels)
INTERSTOP® Gas sealing systems
Steel flow regulation between ladle to tundish and tundish to mould can either be done by slide gate or by stopper control. For both, use of argon can be required depending on the steel grade and the flow control facility. Very little argon flow rate into the stopper and/or nozzle helps to reduce clogging. Additional inert gas shielding around refractory joints exclude any air ingress into the casting channel.
It is apparent, that in this sensitive area close to the end of the phase where steel is still liquid, a very accurate system for the argon control is needed. At this application, very little changes in argon flow will have big consequences: a too small flow will support nozzle clogging, a too high flow will negatively influence the conditions in the mould by introducing too much bubbles.
For this reason Interstop offers very sensitive flow controlled and/or back pressure controlled systems. If you have further questions about our gas sealing systems, please contact us via the “Contact” button below.
Get more information
If you have any questions regarding our Gas and Sealing
Technology, please do not hesitate to contact us. An expert
will contact you in the shortest possible time.