Subscribe to Bulletin
Get notified before everyone else
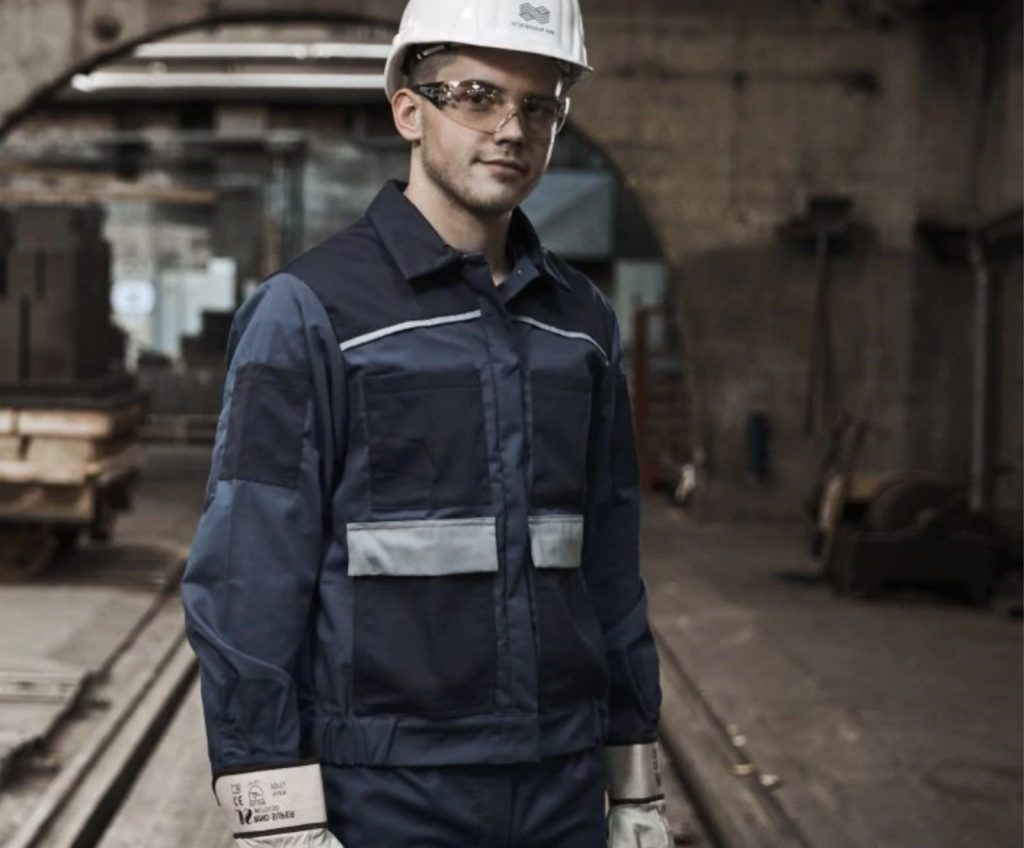
The Bulletin is a scientific trade journal for refractory innovations, in which our specialists inform you about the latest research and development results. In close cooperation with our customers, we report on the latest products and technologies in use. In short: what we do to create benefits for our customers and their processes. As a cross-industry medium for clients, universities, and refractory experts, the Bulletin underlines our claim as technology leader and is evidence of our scientific market leadership.
The steel industry is undergoing a profound transformation as it embraces more sustainable practices, moving towards what many call “green steel”. Today’s refractory industry is at a critical juncture: It must respond to the demands of greener steel, cement, glass, and nonferrous metals production while managing the environmental impact of its own materials and processes. The manufacture and disposal of refractories has traditionally involved energy-intensive processes and nonrenewable materials, but new developments are pointing the way to sustainable, high-performance refractory solutions. One area where refractory development is gaining traction is in the sourcing of sustainable raw materials. For decades, refractories have been primarily produced from nonrenewable resources such as bauxite and magnesite. However, an increasing focus on circularity has led manufacturers to explore more sustainable, often locally sourced, and recycled alternatives. Spent refractories, which were previously discarded as waste, can now be reprocessed and reintroduced into production cycles, reducing dependency on virgin raw materials and mitigating the environmental impact of mining. For example, new technologies, like automated sensor-based sorting, enable the efficient separation and repurposing of used refractory materials, which can then be reintegrated into new products without significant performance loss. This closed-loop approach not only conserves natural resources but also reduces waste generation, aligning the industry with circular economy principles.
High-tech coating technologies, improved bonding agents, and hybrid composites have emerged as promising solutions, providing enhanced durability and chemical resistance. Longer-lasting refractories mean fewer resources are consumed and metallurgical production processes face less downtime, both of which contribute to improved efficiency and reduced environmental impact.
A key pillar of the green steel revolution is the shift toward hydrogen-based direct reduction. Refractories that can withstand the unique demands of hydrogen reducing environments—such as increased resistance to hydrogen and compatibility with hydrogen atmospheres—are essential for this transition. Our researchers are developing refractories tailored specifically for hydrogen-based processes, ensuring that these materials will continue to play a supportive role in the green steel ecosystem. The path towards green steel is challenging, but by investing in sustainable raw materials, energy-efficient production, product durability, and hydrogen-compatible refractories, RHI Magnesita can not only keep pace but also lead the way. This shared journey towards sustainability is not just about reducing emissions; it is about reimagining the industry, securing a healthier planet, and preparing for the future. By fostering a spirit of innovation and collaboration, the refractories industry will continue to be an indispensable partner in the transformation of steel, building a more sustainable tomorrow. Thank you for joining us on this journey into the world of refractories.
Yours sincerely
![]() |
Thomas Prietl
Head of Global R&D and Innovation |
Global efforts towards decarbonisation have recently gained support from various industries…
In order to drive sustainability and contribute to ongoing global green steel transformation initiatives…
Optimum management of steel ladles plays a crucial role for efficient and sustainable steel production…
Desulphurisation in the steel ladle requires a reactive slag with high CaO dissolution…
Flexospheres are a recent product development successfully implemented in fired magnesia-chromite bricks…
Elevating refractory recycling rates to unprecedented levels necessitates enhanced quality control…
The refractory industry plays a pivotal role in various high-temperature industrial processes, such as cement…
Magnesia-chromite bricks are widely used in RH degassers due to their outstanding corrosion and abrasion resistance…
Refractories and flow control systems for clean steel casting are technology drivers…
As the most relined vessel in a steel plant, the tundish can be very time-consuming and work-intensive…
Freeze lining (FL), a protective layer of solidified slag, holds significant economic value in industrial processes…
Reheating furnaces are essential in steel rolling mills to thermally treat blooms, billets, and slabs…