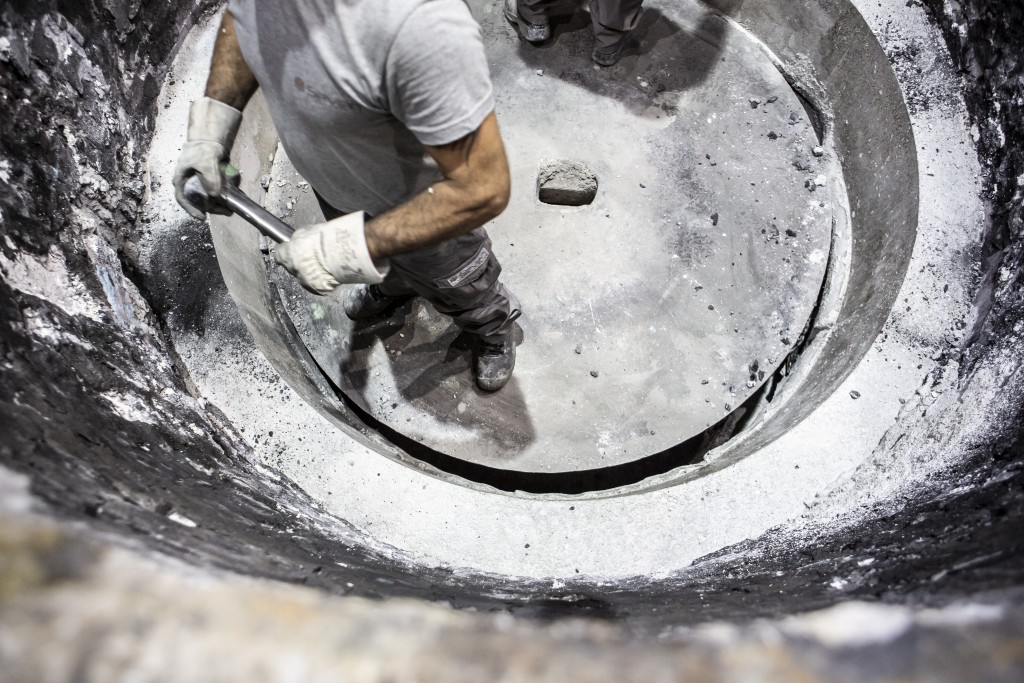
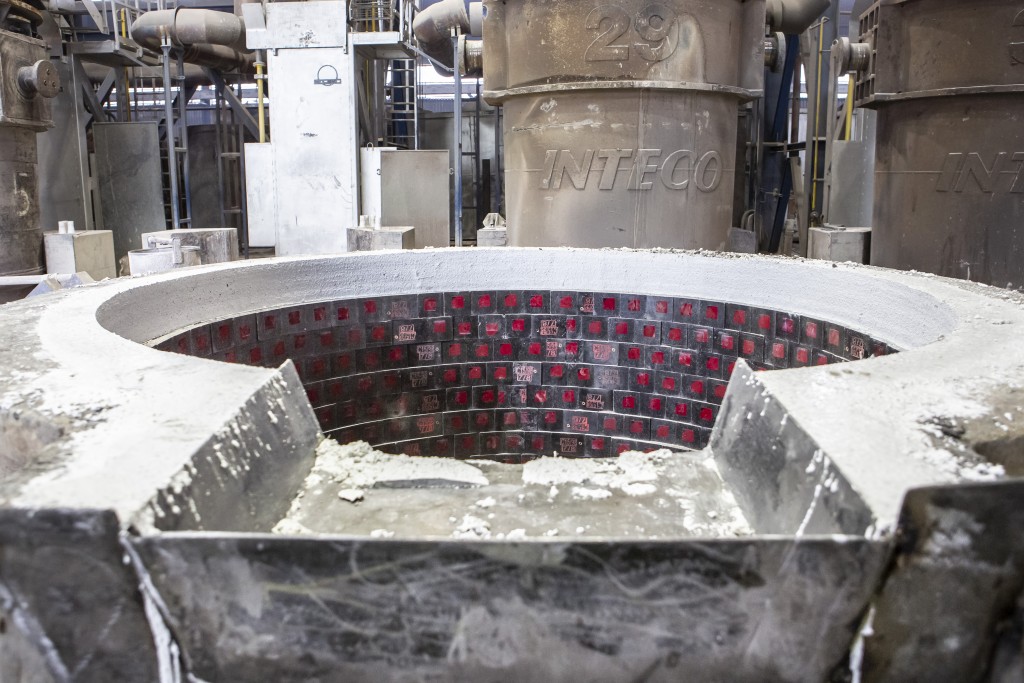
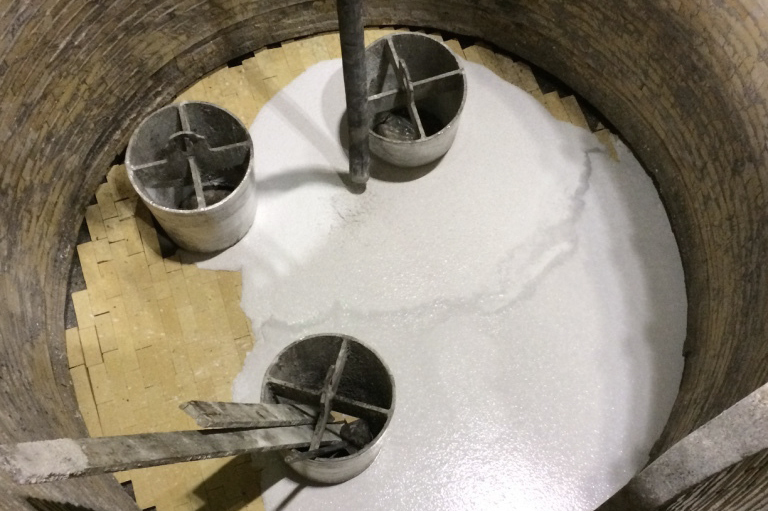
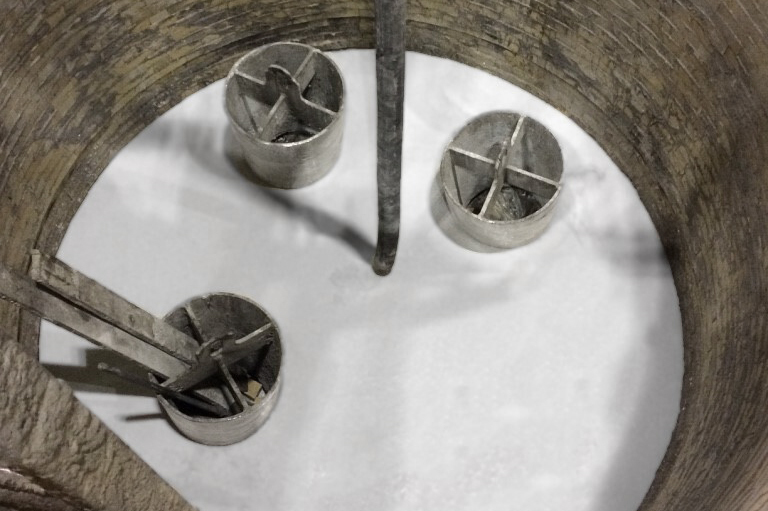
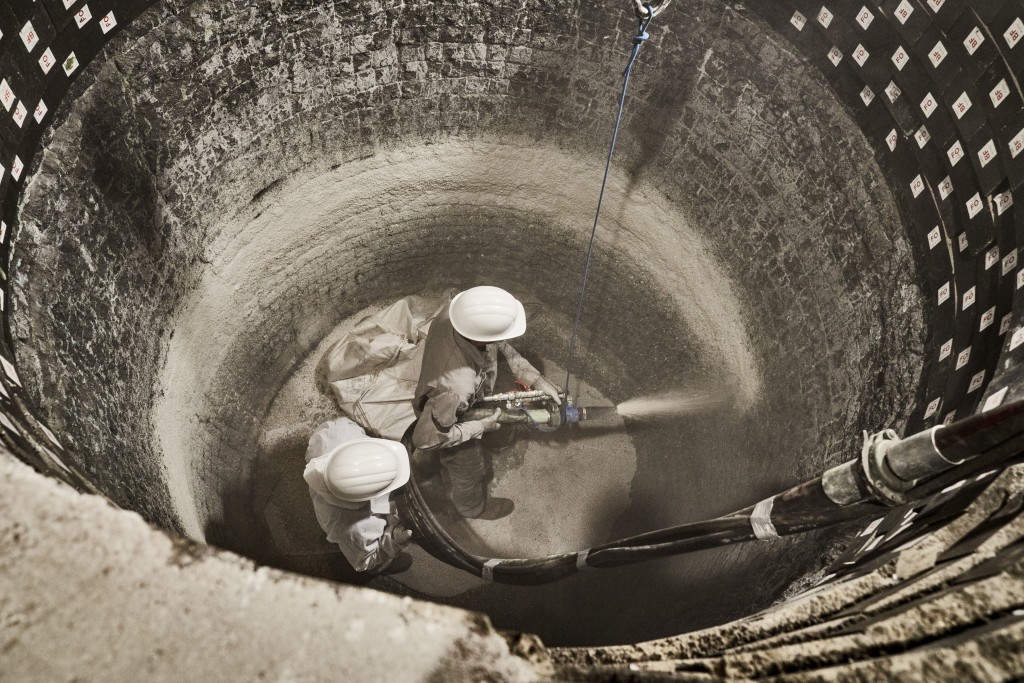
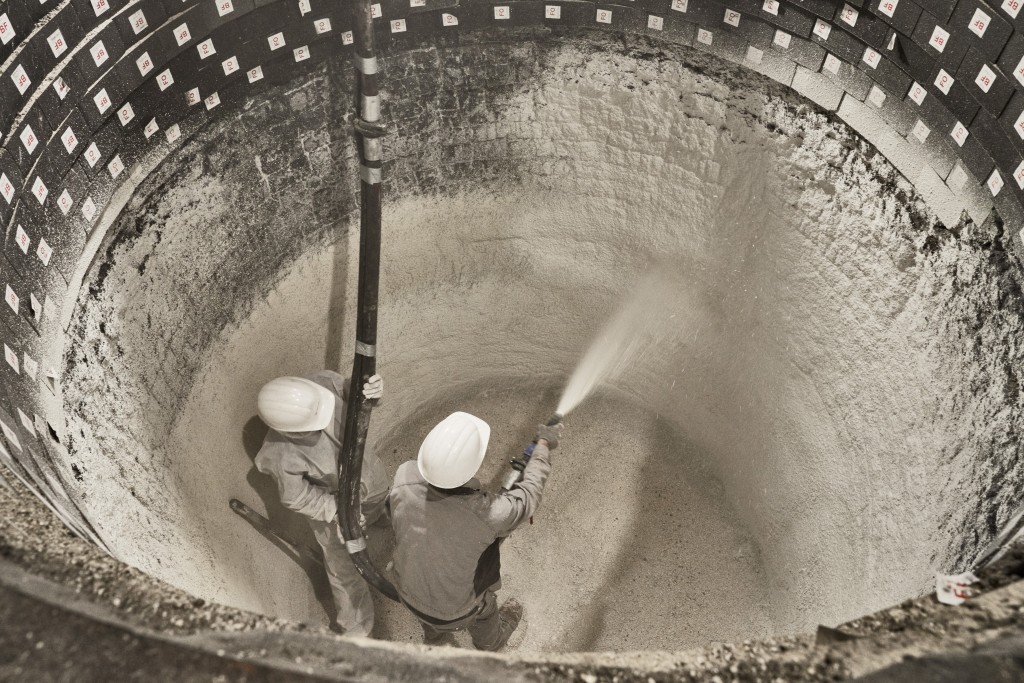
We have supplied a variety of safety and working linings for ladles up to 400 tons capacity.
For the different steel ladle zones and wear mechanisms, Seven Refractories offers a variety of castable materials for vibrating, self-flowing and shotcrete applications.
Reduce the quantity of materials destined to landfill increasing the shares of unshaped in the steelmaking application. Solutions for steel ladle such as monolithic sidewall or maintenance with continuous applications of shotcrete increase the life cycle of the steel ladles and reduce the number of repairs, reducing also the quantity of bricks that have to be disposed in the landfill.
The trials conducted on monolithic ladles have shown that with a combined technology of monolithic sidewall and sequential shotcrete repairs the performance (measured in number of heats) can be doubled.
There are also advantages when it comes to waste reduction and recycling.
2 main features show the benefits of monolithic lining for steel production:
Some of the most modern steel plants in the world are successfully supplied our Smooth Solutions.
Over the past years, advanced monolithic solutions have also become more and more attractive in price when compared with traditional brick installations. As a partner of major steel producers, Seven Refractories has developed technically superior alternatives to bricks.
With Smooth Solutions, a considerable expansion in lifetime and a performance increase in heats could be achieved. Customers benefit from our advanced technology and potential cost reduction.
Alumina-spinel monolithic refractories have been used in steel ladles since the beginning of the 1990’s, but only nowadays the utilization of those materials is becoming a common practice. This concept gives an answer to the different wear patterns due to its unique characteristic in terms of physical and chemical properties.
We have developed several optimized products for different steel ladle zones depending on the dominant wear mechanism:
High resistance to steel and slag contact, compatibility with all types of covering powders, abrasion resistance, high mechanical strength, all coupled together with an enhanced ease of installation, make Smooth Solutions the preferred material for the requirements of modern steel plants.
Joint-free refractory linings substantially improve safety during steel ladle operations as they decrease the risk of leakage and infiltration. While traditional bricks are completely removed at the ladle campaign end, a potentially “endless lining” needs only smaller maintenance repairs.
When the ladle walls are installed with monolithic refractories instead of bricks a potentially thinner layer could be the result. This may increase the productive inner volume of the ladle.
Our Smooth Solutions can also be applied as self-flowing materials where vibrating mixes cannot be easily applied or where casting is not technically suitable.